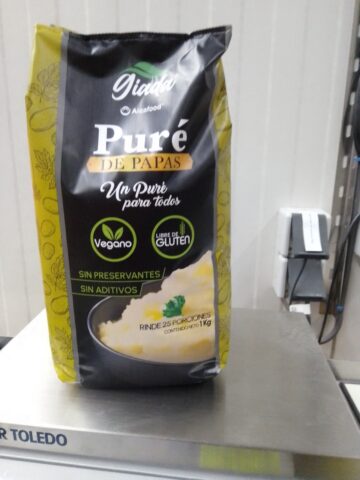
Lamb Weston potato flakes in new packaging from Flexpak
Consumers may not immediately notice it, but in retail – and beyond – plastic packaging, wherever possible, has been getting thinner and thinner for several years. Because thinner means less weight, and therefore less plastic. This also applies to food, where only virgin plastic is allowed. Not recycled, but increasingly recyclable. And for that you need mono material. Flexpak developed such packaging for Lamb Weston.
“In recent years we have been constantly testing whether plastic packaging can be thinner and whether it can be in mono-material. It’s about saving on tonnage and keeping everything perfectly recyclable. Reduction and recycling are the keywords,” says Gert-Jan van Baardwijk, director of Flexpak, one of the now seven subsidiaries of the OPACKGROUP, a group that has grown from Oerlemans Plastics, founded in 1972. Flexpak specializes in printing, laminating and cutting foils. 95% of the company’s turnover is realized in the food sector.
“We laminate multiple layers on top of each other, a process that was still missing within the group by 2016, when we became part of the OPACKGROUP after almost 40 years of independence. Those multiple layers can be, for example, combinations of PET, PP, PE and/or even an aluminum layer. Sometimes such combinations are necessary – an alul layer in the packaging blocks light, a necessary condition for the shelf life of some food products – but packaging consisting of multiple materials is not recyclable or is less recyclable,” Gert-Jan explains.
Sustainable and premium
Lamb Weston, which markets its potato flakes and frozen fries in all shapes and sizes in more than 100 countries. Lamb Weston EMEA has its headquarter in Breda, the Netherlands. At Kruiningen (also Dutch based), the factory delivers the biggest part of the production volume in the EMEA region. The international foodproducer has been a customer of Oerlemans Plastics for a long time. Just over a year ago, the producer of potato products put out a request for laminate packaging for potato flakes for a Latin American customer. That customer itself did not have strict sustainability requirements, says Maite Loyola of Lamb Weston, but it did have visual requirements: “It had to be packaging for a premium line, so the appearance had to be top notch. Its sustainable nature was a requirement from Lamb Weston, as part of our Sustainable Packaging strategy. Our goal for 2030 is to have all our product packaging 100% reusable and/or recyclable. Flexpak managed to combine recyclability with a premium look. That’s quite an achievement, if you ask me.”
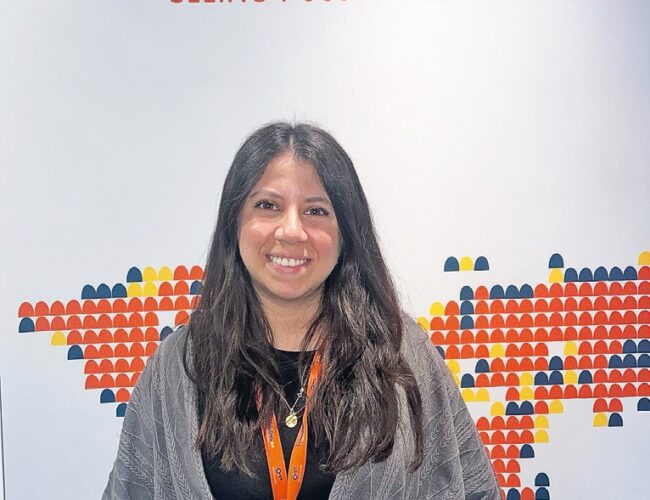
Maite Loyola (Product & Process Manager LambWeston)
The same family
OPE/PE is an innovation from the OPACKGROUP. While in the potato sector a lot of composite materials that are not recyclable are used – think of solutions for long-life mashed potatoes, fresh potatoes in chilled fresh or potatoes from the land – OPE/PE offers a sustainable alternative. “Often two types of materials are glued together because of the different sealing properties of each material. By providing PE, you get a different type of material, called Oriented PE, with different sealing properties. But because both materials are from the same family, the entire packaging is 100% recyclable. And that’s exactly the point,” Gert-Jan explains.
Plastic vs. paper
If society wants to go to 80% recycling in plastics, the plastics expert says we need to put plenty of effort into mono-materials. “The same goes for paper, by the way. Only mono paper is fully recyclable. Solutions such as paper packaging with an alul layer are not, but do have the public’s support, while it is not even entirely clear whether paper, viewed across the entire production, use and waste treatment process, is more environmentally friendly than plastic solutions. There have been several studies on this, but the question is always which factors you take into account in the research. But I think plastic will continue to play an important role in the future. When I was little, the paper was put outside on the street because it was destined for recycling. But my kids now see separate waste collection for plastic as well. Exactly for the same reason. When we are a whole generation away, plastic will have as good a name as paper, because it will all be recycled as well,” Gert-Jan claims.
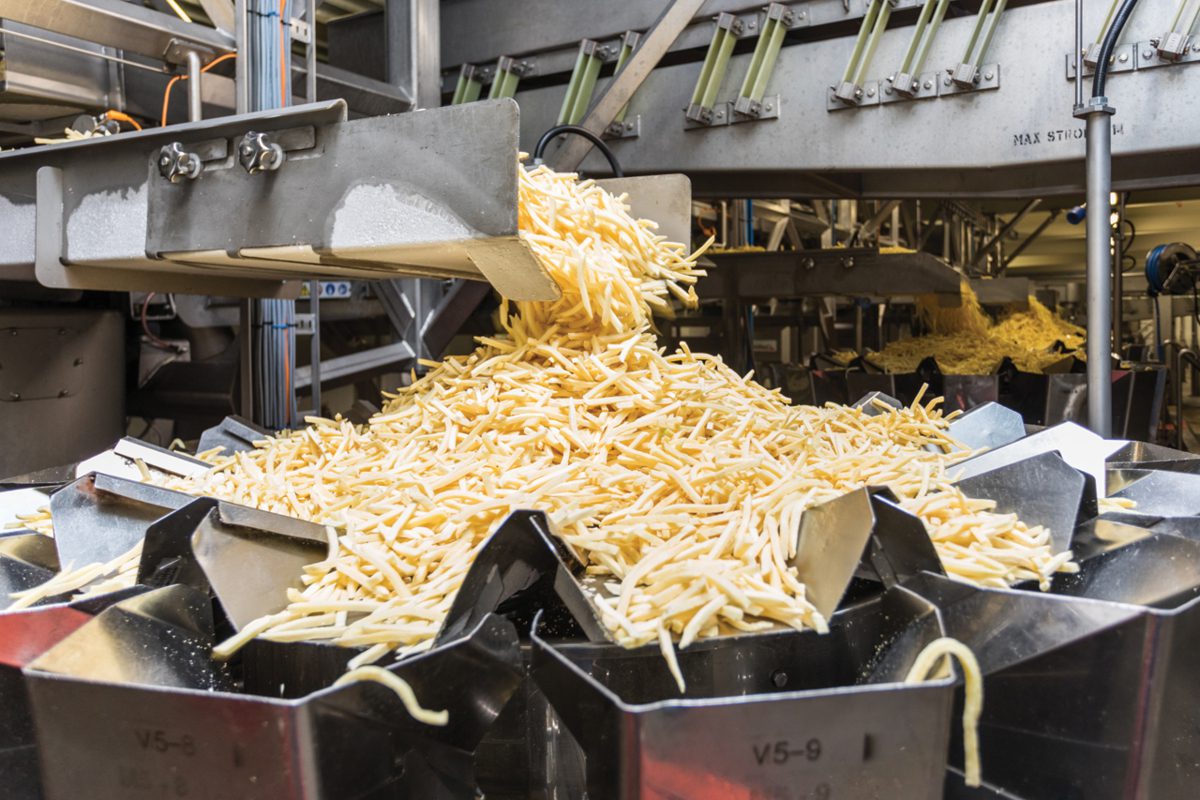
Production image of the LambWeston factory in Kruiningen (the Netherlands)
Discount program
The gradual switch to mono-material packaging in PET, PE, PP or derivatives is being given a boost in the Netherlands by Verpact, formerly ‘Stichting Afvalfonds Verpakkingen’, which takes care of the collective implementation of the mandatory collection, sorting and recycling of their packaging for producers and importers, they know at Flexpak. “There will be a Recycle Check, a tiered discount program where producers and brand owners of plastic packaging get a discount of up to €0.50 per kilogram on their disposal fee if they meet all the recycling requirements. If the label is made of the same material as the rest of the packaging, a dime goes off. If mono-material is used, also a dime off. And so up to €0.50 per kilo discount. So yes, I do see OPE/PE taking off. In about 10 years the supermarket shelves will look completely different. Think also, for example, of less and less printing area on packaging, because the less ink and glue, the better the recyclate after recycling the packaging.”
And to understand that this evolution has now gained momentum, Gert-Jan points out that about seven years ago everything was still laminated on top of each other in the packaging industry. “There was zero demand for mono material. Purchases were often made based on price: the cheapest material offering the best barrier. PET/PE was very popular. The move to monomaterials is quite rapid and it is not always easy. It requires a lot of research and experimentation.”
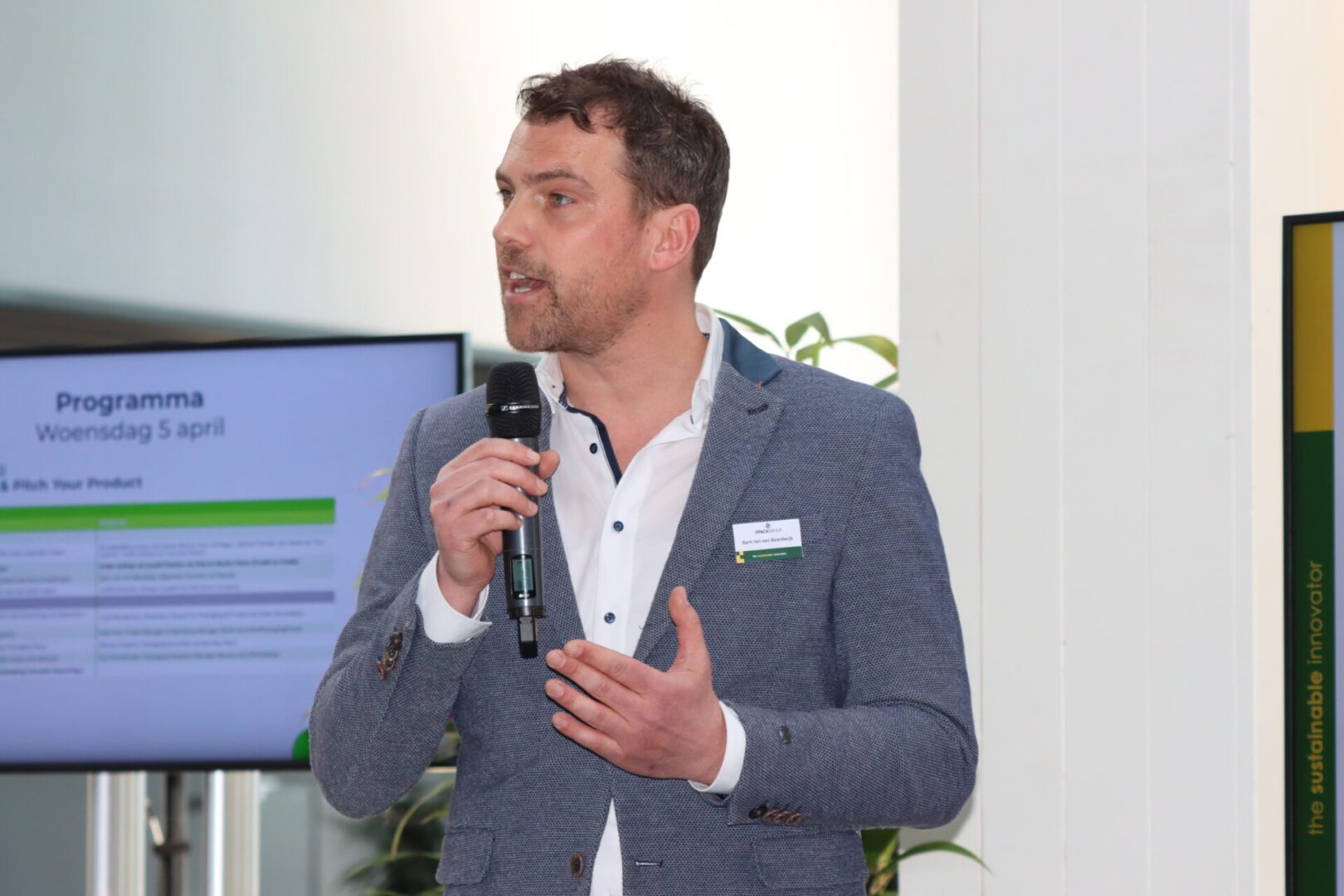
Gert-Jan van Baardwijk (director Flexpak)
One material, but multiple layers
Monomaterial, by the way, does not mean that the packaging would consist of only one layer. “Both the OPE and PE that we laminate both have 7 layers. Both laminates are held together with a very thin layer of glue. But in total, these are therefore 14-layer films. It is, as mentioned earlier, monomaterial because all plastic is of the same family. And the many layers need not be an impediment to keeping the film thin either. The chip bags found in supermarkets today are 32 microns thick, whereas they used to be 65. And although the manufacturing process is more expensive than a few years ago, because you need fewer raw materials, the end result is still slightly cheaper. Anyway, price is not the first concern today. The main question is how to become more sustainable.”
Short chain
About that sustainability, Gert-Jan tells not without some pride that all the OPE/PE in Flexpak’s packaging is made in Oerlemans Plastics’ factory in Giessen. “So no supply chain problems and also no additional transport kilometers due to imports from other countries. Even the printing takes place in the Netherlands. This is certainly an aspect that we like to tell customers and that is appreciated in the current times.”
Thanks to Flexpak’s willingness to think along towards sustainable solutions and Lamb Weston’s full focus on 100% recyclable packaging, a mono-material product has rolled off the line with quality characteristics that also convince customers in Latin America. “All our frozen potato products are already in mono-material packaging,” concludes Maite. “We are now working to achieve the same for our ambient product line. And this new bag for potato flakes is good evidence of that.The plastic runs nicely over the existing machines, there are no problems with tearing and the sealing, our main concern, is perfect.” The benefit of this unique cooperation between Flexpak and Lamb Weston is twofold: there is a gain for the environment and the cost price is lower due to the lesser tonnages of plastic.” (PB/PDC)
For more information:
Gert-Jan van Baardwijk (general manager of subsidiary company Flexpak)