Whereas for years it was complicated in the packaging chain to get all noses in the sustainable direction, now more and more partners in the industry seem convinced of the importance of cooperation. “Retailers and packaging companies are taking more of a lead in sustainable packaging. They are hiring specialists and sustainability managers; no longer does the marketing department just decide which packaging will be on the shelf,” says Merijn Bos, sales director at Oerlemans Packaging Group. The company produces flexible films and packaging made of plastic and, since the acquisition of Stempher this year, also paper. The Oerlemans Packaging Group consists of seven companies, each with its own specialty, and has a highly developed R&D department: the Oerlemans Technology Center (OTC). All seven companies produce for both food and non-food.
Three major challenges
“‘We do sustainability together’ is one of our credos. That’s why, for example, we provide sixteen directors for collaborations within the packaging industry and are active in the Plastic Pact Netherlands, among others,” says sustainability director Rob Verhagen. According to him, the packaging industry is facing three major challenges: “The waste management system leaves much to be desired. Circularity can be better secured and litter must be prevented. In addition, the carbon footprint of packaging must be reduced, throughout the chain. A relevant question, for example, is how a more sustainable design can also save on logistics. And finally, we strive for less use of materials, because overconsumption of raw materials is a major problem. With a focus on the circular economy, we turn waste into raw materials, reduce CO2 and need fewer new raw materials. So circularity is a great tool to achieve the higher goals.”

From composite to mono material
To address these challenges, the company has defined five sustainability directions: re-duce, re-use, re-cycle, re-design and re-new. “Together with customers, we look at what specific problems they face and which solution directions fit. The customer’s strategy is decisive,” says Merijn. “In terms of reduce, we have already made great strides.” Rob continues: “For example, we have developed increasingly thinner films. On barrier and freezer films, for example, as much as 50% reduction has been achieved. Different types of plastic are laminated for this purpose. Many packages now on the shelf, for example, combine PET and polyethylene, or there is PVDC or PA in one of the layers. This gives the packaging a higher barrier, puncture resistance, better processability and also saves on logistics. Super cool of course, but the combined materials cause a disruption in recycling. So we want to return to mono-material polyethylene; that fits best within the recycling system. The new material must have the same properties as the laminated material: a high barrier, good transparency and high rigidity and puncture resistance.”
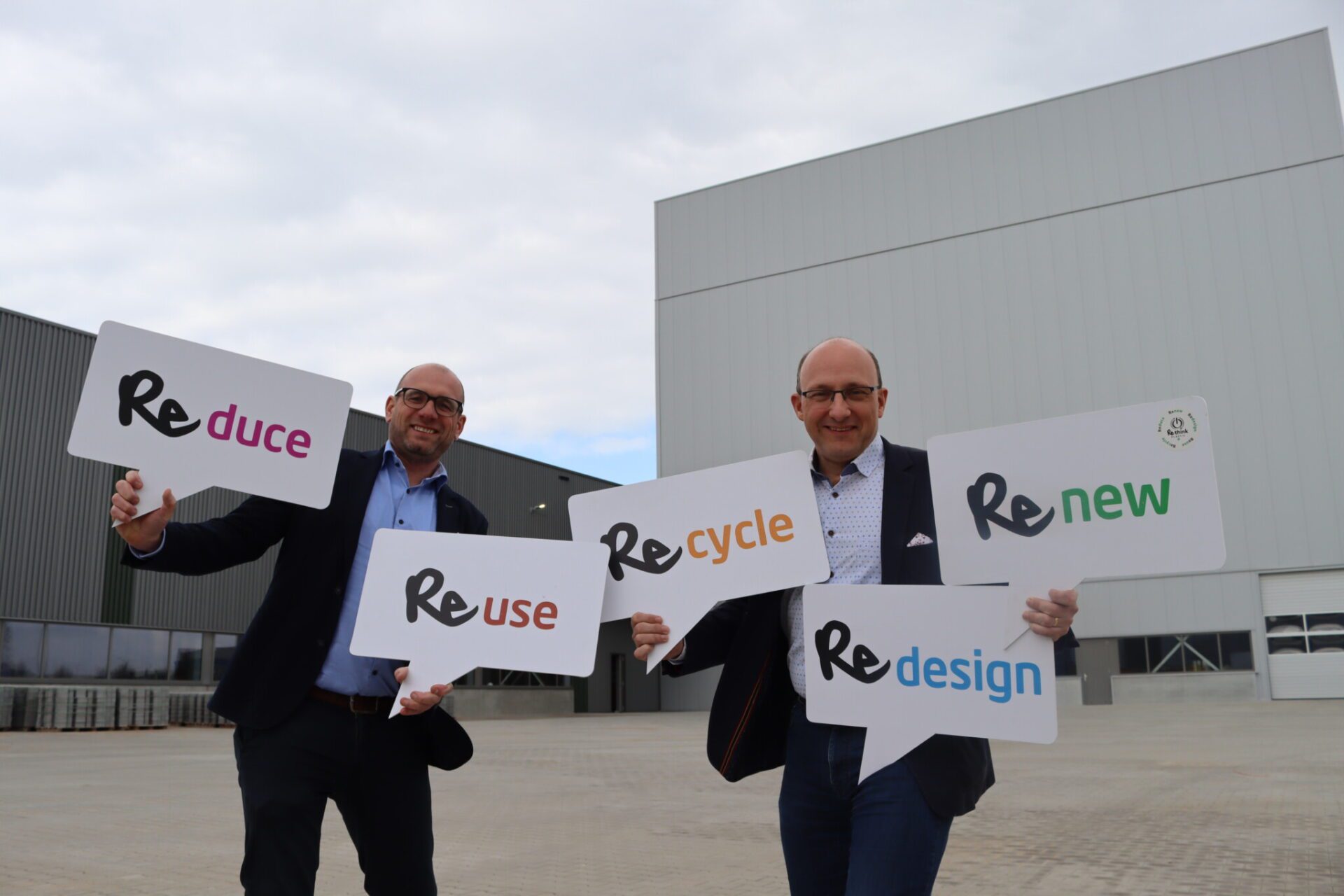
Merijn Bos (l) and Rob Verhagen
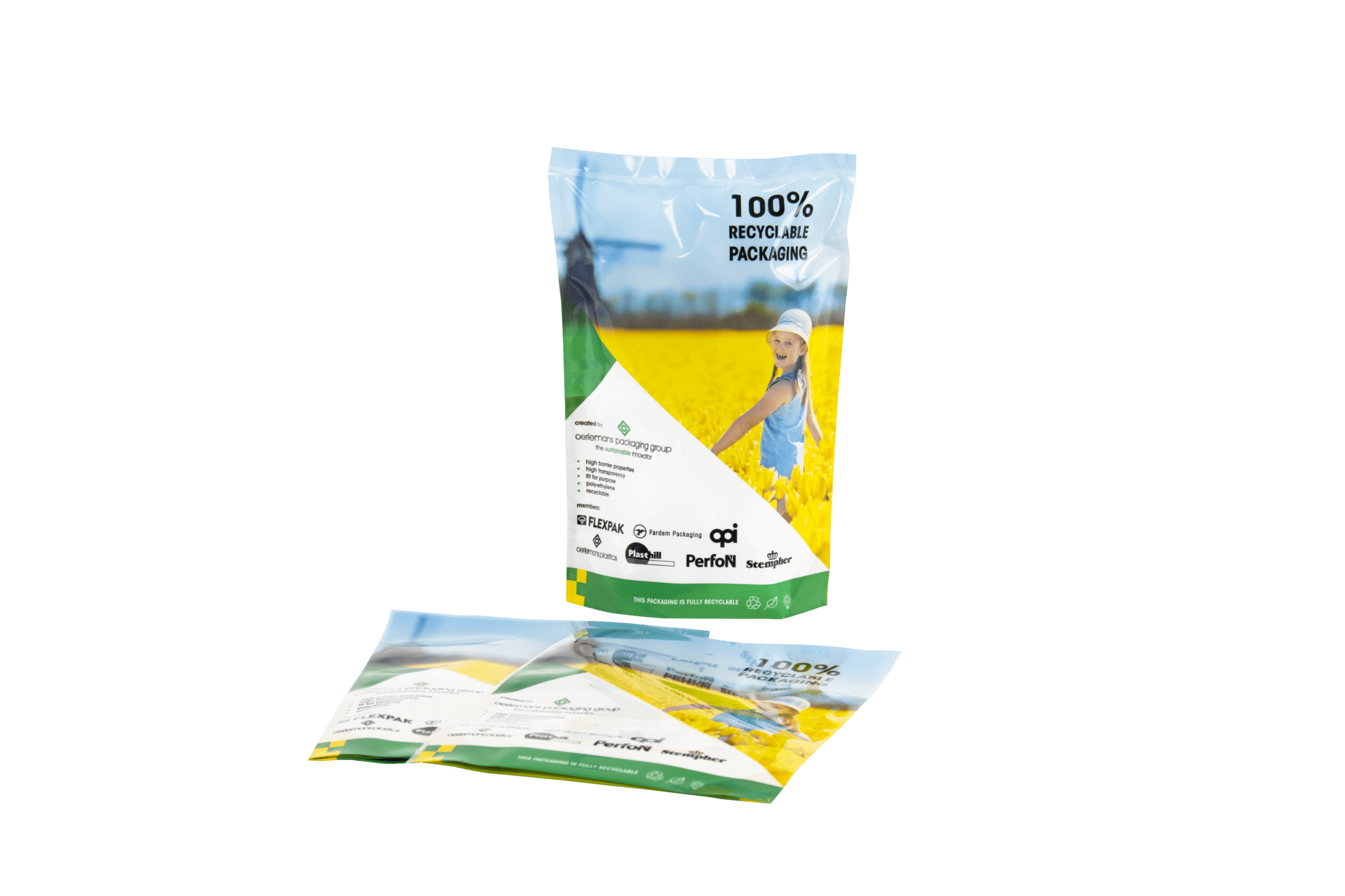
Out in front of the troops
In September, a new plant will open in Giessen, North Brabant, where barrier packaging made of the new material will be produced. The cost of construction is about twenty million euros. “We have invested ahead of the troops because we foresee a huge demand for barrier packaging that is 100% recyclable. Many companies have the goal of working only with recyclable packaging from 2025. Processes and packaging machinery must also be addressed for this purpose. So in the industry, 2025 actually means tomorrow already.”
Lower respiration, longer shelf life
Another innovation – developed in close cooperation with Perfotec – is the Perfotec Linerbag. Merijn explains, “These are bulk packaging for AGF transport, among other things, which are fitted with small laser perforation holes in our special film.” Rob adds: “Fruit and vegetables continue to breathe after harvest – we call that respiration. That varies per crop. If you put just the right amount of holes in the packaging, you greatly reduce respiration and extend shelf life by as much as six to 12 weeks. In addition, this packaging method reduces moisture loss by 10%, which in turn improves quality. And the crops can be transported by ship instead of by plane: lower transport costs and less CO2 emissions in other words. Asparagus, grapes, watermelon and pineapple are already transported with these large overpacks.” What sustainable prospects do they still have for the food industry? Merijn: “To further expand our portfolio with 100% recyclability for all food applications.” Rob: “Closing the chain and making sure that the recyclate that becomes available is used in the best possible way; that’s our biggest challenge in the near future.”
New packaging challenges
Farm Frites serves foodservice operators from more than 100 countries a variety of French fries, potato specialties and appetizers. Together with their partners, the family business has been investing in developing, processing and marketing potato products for more than 50 years. Marketing Director Sander van der Linden: “Sustainability plays a major role in this. We continually challenge ourselves to further minimize the impact of our business operations on the environment. For our packaging worldwide, we strive for less and recyclable, if possible from renewable materials. But while maintaining all functionalities to guarantee the quality of our products. That is the big challenge.”
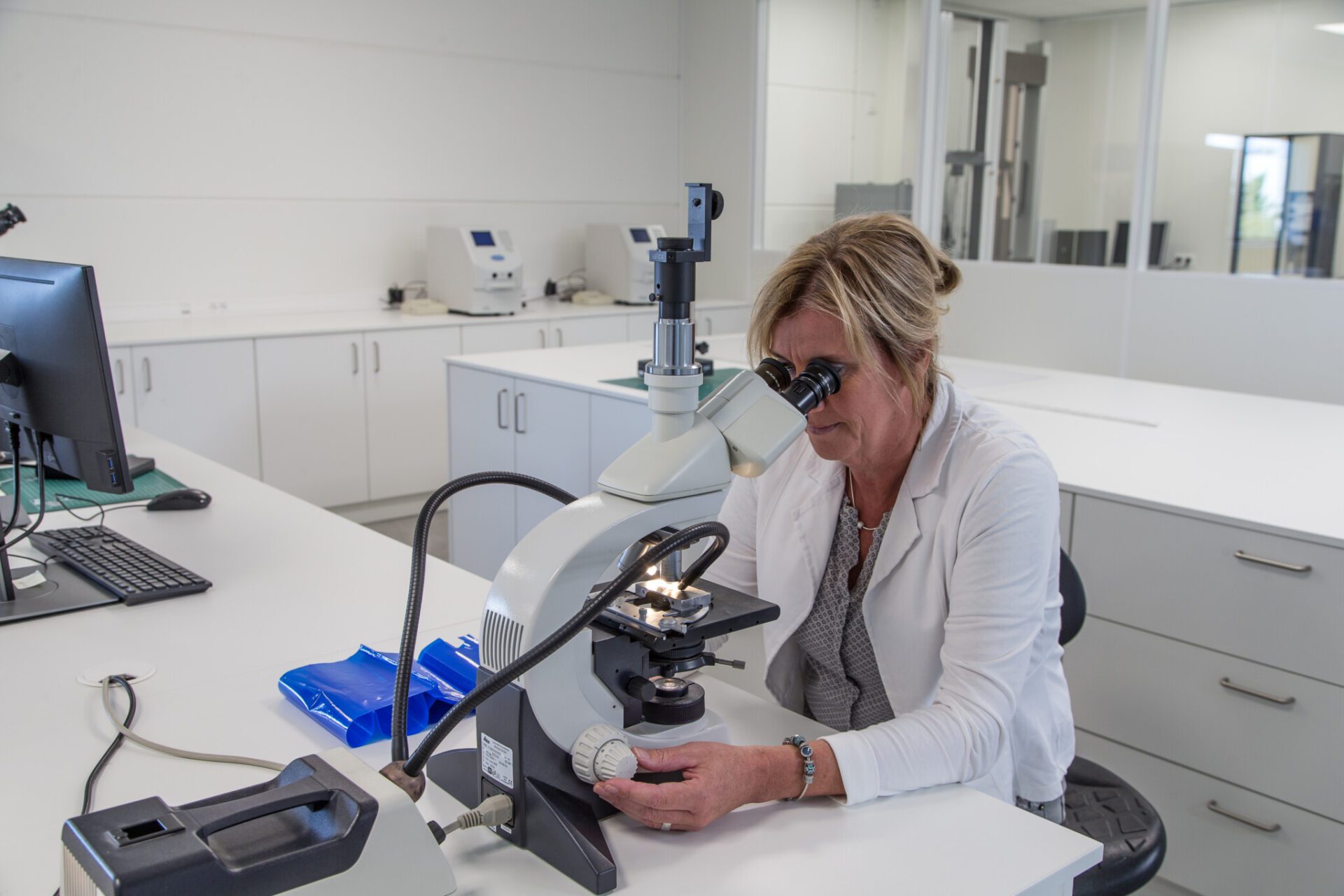
Limits to optimization
“For example, to reduce packaging materials, we look at the type of box that provides the most efficient loading of trucks and shipping containers. This also saves on transport movements and CO2 emissions. We are also investigating whether materials can be made thinner. There are limits to optimization; you lose the intended environmental benefit if the thinner material would lead to product loss or transport damage.”
Good cooperation
Farm Frites is committed to recyclable packaging. This is already the case for frozen products. Over the past two years Farm Frites, together with Oerlemans Packaging, went through an intensive development process to also provide chilled French fries and specialties with recyclable film. “The starting point is the set of requirements we place on the film, such as maintaining product quality and making it more sustainable,” says Sander. “Within this process, good cooperation is essential. You start with development, testing and optimization. A film with good lab results must also continue to perform well during a production run on various packaging machines. Because we pack under a protective atmosphere, seals must remain intact. We do not accept punctures, and the bag must maintain the right ‘look and feel’.”
Further sustainability
Looking to the future, Farm Frites is looking at further use of plant-based and/or recycled materials (recyclate). “The first successful steps have already been taken together with Oerlemans for bags to sample potatoes in storage. These are recyclable, contain recyclate and are reusable several times. For our pilot project we are using their Planet Positive Fries film with plantbased plastic.”
Meanwhile, Farm Frites is experiencing more than ever that the food and packaging world is focused on making the packaging chain more sustainable. Sander: “That demands a lot from the industry, but also from our people, suppliers, machinery and materials. We are proud that together with Oerlemans we can play a role in that transition.
Source: Vakblad Voedingsindustrie